When it comes to lubricant temperature, there is a need for control and
moderation. Finding the right working temperature can extend the
performance and lubricant life. Of course, everything is easy to say, but in
practice can be difficult to do.
Fluid temperature stability is essential for the success of systems
mechanical. All lubricating and hydraulic fluids have maximum limits and
minimum operating temperatures. The machine loses stability and may fail
when the fluid exceeds these limits. If this problem is not treated, the
failures result in degradation of materials and machine components.
In cold weather, lubricants can chemically degrade, separate into phases and
present altered physical states.
Some examples of the consequences of cold on the lubricant:
· “Blended” base oils may begin to separate into phases.
· Paraffinic base oils can become wax gels.
· Some additives may become insoluble resulting in sedimentation.
· Dissolved water can turn into emulsified water (more harmful).
· Many additives that rely on heat-induced chemical reactions do not
are able to act (e.g. EP and AW additives).
· The oil may become more viscous to circulate and the grease more consistent.
· Filters with by-pass open the valve due to the increase in viscosity of the
oil.
In 1903, Svante Arrhenius won a Nobel Prize when he discovered the
relationship between temperature and chemical reaction rates. The so-called “rate rule”
Arrhenius”, refers to the fact that chemical reactions double the reaction rate to
every 10°C increase in temperature. And it's no different with lubricants. A
Once the base activation temperature has been exceeded, the lubricant will
degrade (oxidize) twice as fast for every 10°C (18°F) increase in
temperature. In fact, there are a number of problems associated with excess
heat.
Note: The planet's temperature is on average 2ºC above historical measurements and its effects are being felt in all equipment where these variations are crucial for its correct functioning. The above observation was published in 2021. Now, in 2025, some publications indicate that the planet's average temperature is on average 5ºC above historical measurements and its effects are being felt much more in all equipment where these variations are crucial for its correct functioning.
Some examples of the consequences of high temperatures on the lubricant:
· Accelerates decomposition of oil additive (Arrhenius).
· Some additives will volatilize and escape into the atmosphere.
· Consumes IV more quickly.
· Microbial contaminants prefer warmer temperatures (but not
boiling).
· Heat thins the oil film, causing accelerated wear.
· Hot oil shortens the life of filters and seals and accelerates corrosion.
· Both oils and greases are more prone to leaks.
· Grease separates oil from thickener at high temperatures.
· High temperatures can form carbonaceous and surface resins.
Measuring the temperature of your oil:
Of course, temperature plays a vital role in monitoring the
machine condition and that is why today many Maintenance systems
Predictive have alarms for temperatures. Just as we need to check
our temperature to know if we have a fever, most of the problems
with lubrication, friction and wear will have a temperature profile. So,
in this sense, the change in temperature is good, as we can detect that
something is wrong and we must take quick action.
Creating a temperature measurement route at the most critical points helps to maintain
a good sensitive inspection program.
- Develop temperature limit tables for the most critical equipment,
defining the temperatures from point A to F for the specific location where the equipment
to be monitored is located (e.g. production line) - The normal operating range (Zone 3) is limited by points C and D. Variations in
temperature below point C are controlled by a heater and alarms. The
temperatures above the D line are controlled by coolers and alarms. - Constant operation in zones 2 and/or 4 reduces the life of the equipment and/or
lubricant. Operating in zone 2 may slow the flow of lubricant to the bearings,
increase energy consumption and increase the tendency to foam. Operate in zone 4
can accelerate oil oxidation, reduce the strength of the lubricating film and increase the
wear associated with particles. - Operating in zones 1 and/or 5 threatens machine reliability. Temperatures in
extreme points A and F can cause sudden death of the machine. Zone 1 is a
condition that typically leads to severe lubricant starvation and zone 5 is associated with hazards related to fire, oil degradation, additive depletion,
volatilization and high friction and wear conditions. - The use of synthetic or high IV lubricants helps in areas where there is low or high temperature.
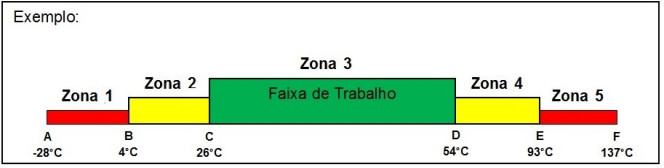